Sistemi Ciberfisici e Digital Twin
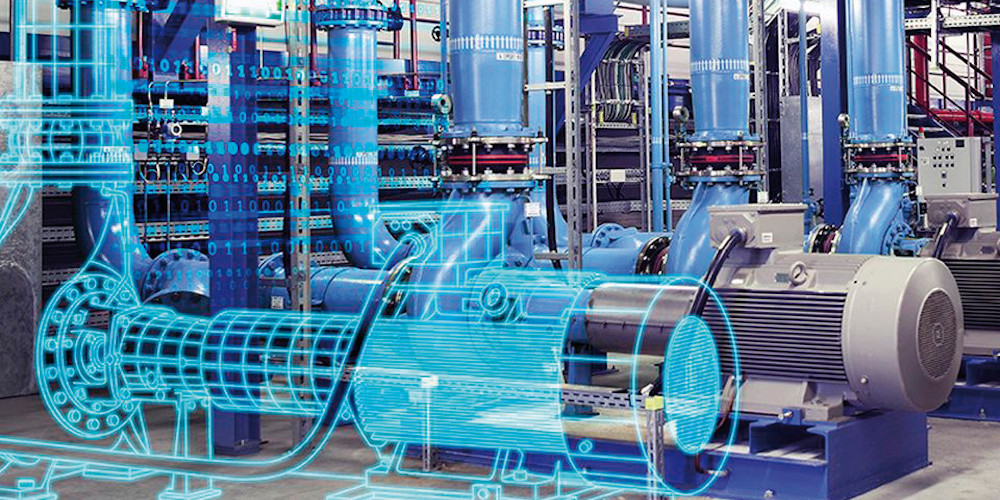
L’evoluzione tecnologica in corso è stata caratterizzata negli scorsi anni da un’estensione dal mondo fisico (mondo degli atomi) a quello virtuale (mondo dei bit), grazie alla creazione di modelli matematici statici (disegni CAD 2D e 3D), modelli dei processi di fabbricazione (CAM) e simulazione dinamica del comportamento di oggetti, macchinari, impianti e processi (CAE).
Il paradigma di Industria 4.0 ha introdotto il concetto di integrazione tra gli oggetti fisici e i loro modelli matematici per mezzo dei sistemi ciberfisici (CPS – Cyber-Physical System): sistemi informatici in grado di interagire in modo continuo con i sistemi fisici a cui sono associati.
Un CPS è composto da un asset fisico dotato di capacità computazionale, di comunicazione e di controllo, che può essere un oggetto, un sistema o un processo industriale (physical twin), a cui è associato un gemello digitale (digital twin) con cui interagisce in modo mono-direzionale (il digital twin acquisisce i dati prodotti dal physical twin, che vengono poi analizzati e utilizzati off-line) oppure in modo bi-direzionale (il digital twin può intervenire con allarmi o in modo diretto sul comportamento del physical twin, se rileva comportamenti anomali o comunque ottimizzabili).
Sistemi sempre più sofisticati
I digital twin consentono sia di monitorare l’attività di un impianto o di un processo sia di prevederne in anticipo i comportamenti.
Si possono realizzare digital twin con vari livelli di complessità, fino ad arrivare a una completa simulazione virtuale di un sistema, prodotto o processo fisico che unisce le informazioni tecniche e gestionali sui componenti e i processi che costituiscono un asset, le caratteristiche tecniche di tutti i componenti, la documentazione collegata al componente (certificazioni, manuali operativi, documenti tecnici, disegni, ecc.), i collegamento tra gli elementi dell’asset e i sistemi di gestione dei documenti, come PDM (Product Data Management) e PLM (Product Lifecycle Management), i sistemi di controllo della produzione come MES (Manufacturing Execution System) o DCS (Distributed Control System), fino ai sistemi di gestione ERP (Enterprise Resource Planning), per integrarli in tempo reale con i dati di processo. I sistemi più evoluti sono basati su reti neuronali e algoritmi di intelligenza artificiale che individuano comportamenti anormali confrontando i dati provenienti dai sensori con i modelli predittivi e si avvalgono di interfacce uomo-macchina (HMI – Human Machine Interface) basate su ambienti di realtà virtuale e realtà aumentata per comunicare con gli utenti in modo immediato e immersivo.
Gli utilizzi
L’utilità del digital twin è trasversale a tutte le industrie manifatturiere operanti nei più diversi settori industriali, per arrivare agli edifici intelligenti controllati dai sistemi BIM (Building Information System) e alle Smart Cities. I settori particolarmente interessati dall’implementazione di un gemello digitale sono la progettazione, il controllo di produzione e della qualità, la manutenzione e in generale i servizi post-vendita.
I vantaggi
L’obiettivo principale di un digital twin è rispondere immediatamente ai cambiamenti esterni per:
• anticipare e prevenire problemi;
• risolvere i problemi tempestivamente, effettuando nel mondo virtuale tutte le modifiche necessarie per garantire che l’asset fisico lavori esattamente come previsto;
• risparmiare tempo e denaro nelle fasi di simulazione, test e analisi e accelerare il time to marketing;
• migliorare le prestazioni del gemello fisico. La possibilità di monitorare i prodotti durante il loro funzionamento consente di verificarne le funzionalità e come queste sono utilizzate, e permette di continuare il testing in situazione di uso reale per affinare il prodotto e aggiornare in tempo reale il software embedded nel prodotto;
• il modello digitale può anche essere utilizzato per fare test di durata, accelerando lo scorrere del tempo in modo da valutare in alcune ore diversi anni di operatività. Se si presenta un problema, il tempo può essere ‘rallentato’ per permettere al progettista di osservare quello che succede nei momenti critici;
• la presenza di digital twin apre anche, potenzialmente, uno spazio per terze parti, come assicurazioni, PMI e start up, che possono sviluppare servizi basati sulle informazioni prodotte dai digital twin e creare nel tempo un ecosistema interconnesso.
Alcuni esempi
I produttori di automezzi, navi e aerei, costruiscono modelli digitali su cui effettuano tutte le prove e le simulazioni necessarie ad arrivare a un progetto soddisfacente (prototipazione digitale). Quando il modello digitale è pronto, si convertono i bit in atomi con vari tipi di macchine (come le stampanti 3D) e si ottiene il prototipo.
Questo processo può coinvolgere tutta la catena logistica. Per esempio, produttori di aerei come Boeing inviano ai fornitori le specifiche digitali delle parti con cui il loro componente dovrà interfacciarsi, e questi a loro volta devono fornire al committente una rappresentazione digitale del componente che dovranno realizzare. Il produttore effettua l’integrazione a livello digitale di tutti i componenti, esegue test e simulazioni e, dopo avere verificato il corretto funzionamento dei modelli, attiva la produzione propria e dei fornitori. Con il virtual commissioning si può valutare il comportamento dell’automazione di un sistema ancora prima di avere il prodotto assemblato, verificandone a priori la bontà e la consistenza.
General Electric da alcuni anni ha esteso l’utilizzo dei modelli digitali delle sue turbine (sia quelle utilizzate nei sistemi eolici sia quelle che operano nei turboreattori) alla loro manutenzione e controllo. La turbina viene venduta associata al proprio digital twin: un modello digitale specifico di quella turbina. La turbina fisica contiene vari sensori che inviano alla turbina virtuale tutti i dati relativi al funzionamento, come velocità di rotazione, potenza istantanea, temperature, pressioni, vibrazioni, etc. Questi dati consentono al digital twin di simulare la situazione operativa e di rilevare eventuali difformità di funzionamento tra il modello virtuale e la turbina fisica, che fanno scattare meccanismi di controllo per identificare e risolvere il problema.
Ogni automobile Tesla ha a bordo un gemello digitale. Tesla riceve ogni giorno informazioni da centinaia di migliaia di auto (oltre 2 milioni di km al giorno, sommando i contributi di tutte le auto). Questa enorme mole di dati consente di verificare e risolvere la presenza di problemi dipendenti dalla progettazione.
Il mercato dei digital twin
I CPS stanno entrando nell’utilizzo mainstream, rappresentano uno strumento primario per le organizzazioni che implementano progetti IoT e stanno diventando parte integrante delle strategie digitali. I principali protagonisti del mercato dei digital twin sono grandi gruppi industriali come General Electric, IBM, Robert Bosch, Siemens e software house come ANSYS, Dassault Systèmes, Microsof, Oracle, PTC e SAP, oltre a decine di aziende minori e start-up.
IDC prevede che il mercato globale dei digital twin crescerà dai 3,8 miliardi di dollari nel 2019 fino a 35,8 miliardi nel 2025, e che nel 2022 il 40% dei vendor di piattaforme IoT integreranno nella loro offerta sistemi di simulazione in grado di creare digital twins e il 70% dei produttori industriali useranno queste tecnologie per effettuare simulazioni, valutazioni di scenari e sistemi di manutenzione predittiva, riducendo del 30% i fermi per guasti.
Secondo Gartner, il 13% delle organizzazioni che implementano progetti IoT utilizzano già digital twin, mentre il 62% prevede di farlo, mentre entro il 2022 oltre due terzi delle aziende che implementano l’IoT avranno installato almeno un digital twin in produzione.