La strada verso la convergenza
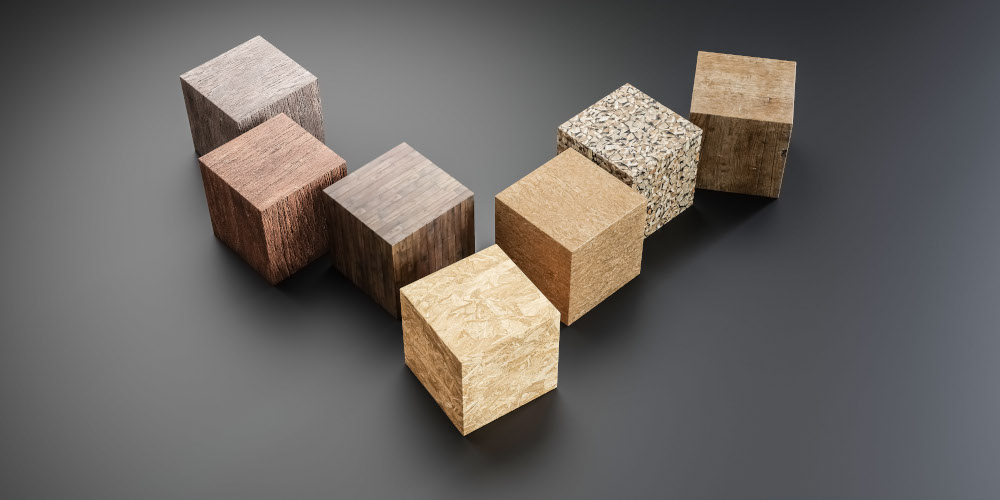
La quarta rivoluzione industriale ha portato profondi cambiamenti nell’industria manifatturiera grazie a tecnologie abilitanti, in larga parte pre-esistenti, che oggi consentono di apportare un valore aggiunto collaborando tra di loro in sistemi integrati (Smart Manufacturing). Attualmente, tra il livello gestionale e quello produttivo esiste ancora un notevole gap di natura culturale, sistemistica e tecnologica. Il processo di avvicinamento e integrazione tra questi livelli è però indispensabile per migliorare la flessibilità e la reattività delle aziende, per resistere meglio alla competizione e alle fluttuazioni di un mercato globalizzato.
In particolare, il mondo dei sistemi informativi (IT) e il mondo dell’automazione industriale (OT) sono ancora gestiti in maniera separata sotto l’aspetto organizzativo, comunicano poco tra di loro e sono due entità indipendenti, ognuna con i propri silos informativi. L’integrazione tra IT e OT coinvolge aspetti sia organizzativi che tecnologici. A capo dell’IT c’è generalmente un CIO (Chief Information Officer), nell’OT un COO (Chief Operating Officer), che procedono in modo indipendente. Oggi le soluzioni tecnologiche a disposizione permettono una sinergia di queste funzioni e aprono opportunità per creare innovazione in molti settori industriali e pubblici (come aziende manifatturiere e logistiche, utility, energia, smart grid e smart cities) che possono trarre giovamento dall’integrazione fra IT e OT.
L’integrazione IT/OT combina i reparti di informatica (Information Technology, IT) e di tecnologia operativa (Operational Technology, OT) in un unico sistema tecnologico in cui l’IT si occupa della gestione dei dati e delle informazioni digitali di computer, software e reti all’interno di un’organizzazione, mentre l’OT si occupa del monitoraggio e del controllo dei dispositivi, dei macchinari e dei processi industriali. Quando l’IT e l’OT vengono gestiti congiuntamente, i processi e i flussi di informazioni risultano semplificati.
I sistemi IT gestiscono i dati
IT (Information Technology, Tecnologia dell’Informazione). Gestisce l’insieme delle tecnologie e delle infrastrutture per l’elaborazione delle informazioni, che includono:
• Hardware. Data Center, server, sistemi di archiviazione, dispositivi degli utenti finali fissi e mobili
• Reti di comunicazione (networking). Apparati attivi e passivi delle reti locali e geografiche, servizi basati su cloud, connettività a Internet e i loro servizi correlati (Cyber Security, etc).
• Software. Tutte le applicazioni utilizzate per la creazione, l’archiviazione, la sicurezza, la condivisione e l’elaborazione dei dati.
Il ruolo dell’IT è ampio ed estremamente diversificato, in quanto comprende sistemi che controllano e tracciano le attività contabili, il marketing, le vendite, l’assistenza ai clienti, la logistica e le risorse umane.
I sistemi OT controllano il mondo fisico
OT (Operational Technology, Tecnologia Operativa). Utilizzata principalmente in ambito industriale nei sistemi di controllo della produzione e delle infrastrutture, nei trasporti e nelle società di servizi. Monitora e controlla le prestazioni dei dispositivi fisici: l’insieme dell’hardware, del software e delle reti utilizzati nei sistemi di controllo industriali, di produzione e di processo, che rilevano o provocano delle modifiche attraverso il monitoraggio e il controllo diretto di dispositivi fisici, processi ed eventi all’interno di una struttura. A differenza dell’IT, l’OT si occupa principalmente della gestione e del controllo delle risorse fisiche, anziché dell’elaborazione dei dati, della comunicazione o della gestione delle informazioni. L’OT è comunemente presente in settori quali la produzione, l’energia, le utility, i trasporti e le infrastrutture critiche come gli impianti di trattamento delle acque e le reti elettriche.
I dispositivi che fanno capo alle reti OT vanno dai sensori, relè e altri circuiti installati nei macchinari e negli impianti ai controlli delle celle di produzione (Edge Computer) ai terminali portatili degli utenti finali. Nella maggior parte dei casi, l’OT supporta apparecchiature specializzate che acquisiscono e trasmettono dati per consentire alle attrezzature industriali di eseguire compiti specifici.
Le reti industriali M2M (Machine to Machine) sono nate per gestire il controllo di apparati e sono quindi progettate per avere basse latenze, ricezione garantita di pacchetti e comportamento certo e affidabile. I sistemi OT possono utilizzare controllori logici programmabili (PLC), sistemi di controllo di supervisione e acquisizione dati (SCADA), sistemi di controllo distribuiti (DCS), sistemi di controllo industriale (ICS) e altre tecnologie. I PLC (Programmable Logic Controller) utilizzati per il controllo delle macchine industriali, convertono i segnali acquisiti dai sensori in valori numerici. Molti degli strumenti per il monitoraggio o la regolazione dei dispositivi fisici erano meccanici e quelli che avevano controlli digitali utilizzavano protocolli chiusi e proprietari.
L’OT ha avuto negli ultimi anni un’evoluzione simile a quella dell’IT, ma si concentra sui dispositivi fisici che controllano le operazioni e i processi industriali, mentre l’IT si concentra sui dati. Tuttavia, poiché i dispositivi fisici stanno diventando sempre più intelligenti, si registra una tendenza crescente alla convergenza IT/OT. I progressi nella comunicazione M2M e nel machine learning consentono di analizzare in tempo reale i dati prodotti dai dispositivi fisici per facilitare l’autonomia, la manutenzione preventiva e il miglioramento dei tempi di attività.
Differenze tra OT e IT e modalità di interazione
OT e IT sono entrambe tecnologie basate su reti che collegano tra loro centinaia o migliaia di apparecchiature, ma al di là della topologia di base, ci sono notevoli diversità. I dispositivi hardware utilizzati nei controlli industriali generalmente hanno una minore potenza di calcolo ma sono più robusti e affidabili, poiché privilegiano la Business Continuity, ed è per questo che tipicamente un PC industriale ha una CPU meno potente e meno memoria di un PC da ufficio, ma ha una disponibilità (Uptime) maggiore. Qualche minuto di fermo per un sito web o per il software gestionale è un problema, meno critico dell’interruzione di una linea di produzione (vedere tabella a lato).
Le reti IT utilizzano in genere sistemi operativi standardizzati, come Linux e Windows. Gli ambienti industriali che supportano l’OT oltre i sistemi operativi delle reti IT, utilizzano anche sistemi operativi proprietari personalizzati per determinati processi industriali. A livello di rete, la tecnologia Ethernet e i protocolli di trasmissione TCP/IP sono un modello oramai consolidato da anni nell’ambito IT. Viceversa la parte OT utilizza anche reti industriali come DeviceNet, CAN e Profibus/Profinet e protocolli come OPC/UA e MQTT. Le dimensioni dei dati e la velocità con cui vengono trasmessi, analizzati e utilizzati nelle reti OT e in quelle IT sono diverse. L’OT è più incentrato sui singoli dispositivi rispetto all’IT e utilizza i dati in tempo reale per monitorare e controllare i device fisici, per garantire che i processi si svolgano correttamente senza interruzioni. L’IT è incentrato sugli utenti e sui dati e spesso utilizza dati storici per analisi relative all’assistenza clienti, ai rapporti di back office, al marketing, etc.
Le imprese 4.0 integrano le tecnologie IT con quelle OT creando reti multi-livello in cui ogni strato è gestito con la tecnologia più opportuna. In questo scenario, la tecnologia IT viene utilizzata soprattutto per uniformare la comunicazione fra i livelli e fra le varie reti OT, aventi strutture e protocolli diversi.
I gateway industriali IoT (Internet of Things) sono nodi di interfacciamento fra OT e IT, che parlano da un lato la lingua dell’OT, traducono questi segnali legati all’ambiente fisico in segnali adatti all’IT e quindi al modello concettuale della fabbrica e poi li inviano nella rete IT. Questo rende possibile la creazione dei Sistemi Cyber-Fisici (CPS, Cyber Physiscal System) e dei “Digital Twin”.
Vantaggi della convergenza IT/OT
La convergenza IT/OT implica l’integrazione di due reti distinte e la condivisione dei dati che ciascuna di esse raccoglie e distribuisce. Molti dei dati relativi alle macchine e ai processi raccolti dai sistemi OT, possono essere utili all’azienda per le previsioni, la pianificazione e il controllo della catena di fornitura. Inoltre, l’OT può utilizzare i dati aziendali dell’IT per regolare i processi di produzione ai fini di una maggiore efficienza. Un altro vantaggio della convergenza è la riduzione dei costi. Unendo le reti e gestendo l’OT in una sottorete sicura, è possibile ridurre la quantità di apparecchiature di rete necessarie, poiché alcune parti della rete convergente serviranno sia il lato industriale che quello gestionale dell’azienda.
Una rete fisica convergente facilita la condivisione dei dati, e le risorse di archiviazione dei dati possono essere unificate. L’IT e le unità aziendali che supporta sono più efficienti quando i dati dell’OT sono incorporati in tempo reale nelle banche dati centrali, consentendo pratiche come migliori analisi (Business Intelligence), produzione just-in-time, gestione più efficiente della supply chain, maggiore agilità e flessibilità e decisioni più rapide e informate. La convergenza IT/OT è un pilastro della manifattura intelligente.