Evoluzione del software per l’Industria 4.0
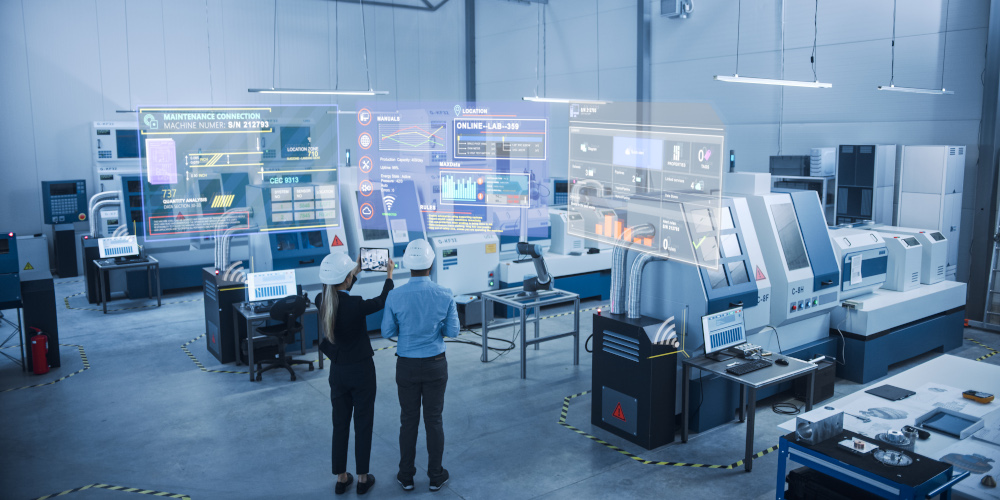
La diffusione del modello Industria 4.0 ha portato a un maggiore utilizzo di tecnologie digitali e smart device nonché a un cambiamento del modo di pensare, progettare e realizzare i processi produttivi. Le tecnologie digitali erano già presenti nelle fabbriche a partire dagli anni ’70, ma con Industria 4.0 il software assume un’importanza predominante a tutti i livelli, poiché è il cuore e il cervello delle principali tecnologie abilitanti (Key Enabling Technologies – KET’s): dal software embedded nelle macchine utensili a controllo numerico, nei robot e nei PLC che controllano i centri di lavoro ai sistemi di gestione delle supply chain, dal firmware che controlla sensori e oggetti intelligenti all’IoT e al cloud, dai sistemi per il controllo di qualità all’analisi dei big data.
Nei livelli più bassi, quelli più vicini alle macchine e agli impianti, l’aspetto più importante sono i tempi di risposta in tempo reale, e quindi la disponibilità di comunicazioni veloci e di potenza di calcolo vicina alla produzione (ioT ed Edge Computing), mentre ai livelli più alti è importante la capacità di trattare grandi masse di dati e problematiche complesse (big data e intelligenza artificiale).
Il software industriale si espande sia a livello orizzontale, collegando e integrando i vari silos applicativi delle aziende (sistemi di progettazione, simulazione, produzione, automazione, logistica, sistemi gestionali, CRM, sistemi direzionali, etc), sia a livello verticale, scalando tutti i livelli dei sistemi informativi, e supporta le industrie manifatturiere e di processo per renderle più veloci, flessibili ed efficienti.
Una produzione più flessibile, una maggiore produttività e lo sviluppo di nuovi modelli di business sono oggi possibili grazie alle soluzioni digitali. Inoltre, le tecnologie all’avanguardia creeranno nuove opportunità per le industrie discrete e di processo, per soddisfare le specifiche esigenze dei loro clienti.
Una nuova generazione di soluzioni
Per questo sono nate soluzioni software specifiche in grado di orientare la produzione in maniera flessibile, che re-ingegnerizzano i processi fisici e logistici sfruttando le funzionalità delle tecnologie digitali con lo scopo di aumentarne l’efficienza e l’efficacia. I software per l’industria 4.0 aumentano le connessioni tra uomini, strumenti e macchine della smart factory. Raccolgono e scambiano informazioni per mezzo di sistemi informativi. Utilizzano i big data, l’analisi predittiva e l’intelligenza artificiale, tre strumenti fondamentali per le aziende che vogliono garantirsi un alto livello di competitività sul mercato. Le principali funzioni di questi programmi sono:
• Progettazione di prodotti intelligenti. Lo sviluppo di un nuovo prodotto, la pianificazione di un nuovo impianto o la produzione con l’aiuto di strumenti digitali crea un’immagine virtuale dettagliata, il digital twin. Il ‘gemello digitale’ permette di ottenere utili informazioni, grazie alla combinazione di simulazioni della realtà basate sull’analisi dei dati in un ambiente virtuale. Ciò consente di creare innovazione più rapidamente e in modo più affidabile, richiedendo al contempo un numero significativamente inferiore di prototipi reali. Quando viene realizzato il prodotto o quando un impianto inizia a funzionare vengono prodotti dati sulle prestazioni della produzione e del prodotto reale che possono essere raccolti, analizzati e riportati nella fase di sviluppo. Ciò contribuisce a migliorare e ottimizzare i nuovi prodotti e i processi già dalle fasi iniziali.
• Programmazione della produzione. Pianificazione e ripianificazione degli ordini di produzione, pianificazione dei carichi di lavoro delle singole risorse, elaborazione delle statistiche riguardanti i carichi di produzione e rappresentazione grafica degli andamenti e dei trend.
• Schedulazione della produzione. Organizzazione delle operazioni per ottenere un piano fattibile rispettando i vincoli di produzione, le date di consegna e la disponibilità delle risorse.
• Raccolta dati. Per adeguare velocemente la produzione ai cambiamenti di mercato le aziende necessitano di adeguare i processi produttivi. Raccolta precisa e puntuale in tempo reale dei dati per la gestione dei processi, il monitoraggio, il controllo e l’avanzamento della fabbrica confrontando l’andamento delle attività programmate con i dati racconti in produzione.
• Monitoraggio della produzione. Il monitoraggio in tempo reale di tutte le fasi produttive ne migliora l’efficienza grazie alla raccolta e all’analisi dei dati. Si possono verificare le performance di specifici gruppi di lavoro, singoli addetti, macchine e impianti.
• Gestione della logistica di magazzino. Consente di migliorare la logistica di magazzino ed è una soluzione specifica per le attività produttive. Dall’allocazione dei prodotti alla loro ubicazione dinamica in fase di acquisto, fino al transito in produzione interna e ai terzisti. Valutazione di materie prime, semilavorati, work in progress e prodotti finiti rispetto ai costi fiscali, gestionali. Tracciabilità e rintracciabilità dei materiali.
• Configurazione dei prodotti. Velocizza e semplifica i processi di configurazione del prodotto, ottimizzando i processi commerciali e tecnici. Il configuratore di prodotto è uno strumento che agevola la preventivazione riducendo errori e tempi d’attesa. Riduce il time to market abbreviando i tempi di progettazione, creando in automatico le distinte base e i cicli di lavoro dei prodotti configurati.
• Gestione delle attrezzature. La corretta gestione di utensili e attrezzature aumenta la produttività, migliorando l’uso delle macchine e riducendo i costi di magazzino. Gestisce la codifica, i dati tecnologici, la logistica e la disponibilità degli utensili.
• Gestione della manutenzione. La manutenzione predittiva su macchine e impianti aiuta a mantenere un elevato di standard qualitativo e di rendimento, il rispetto delle consegne e abbassa i costi di manutenzione straordinaria. La telemanutenzione e l’utilizzo di applicazioni di realtà aumentata e realtà virtuale snelliscono gli interventi tecnici e riducono i tempi di fermo di macchine e impianti.
• Controllo qualità. Controllo e gestione della qualità in produzione e in accettazione fornendo le procedure per la gestione delle non conformità.
Le aziende manifatturiere e di processo hanno iniziato a investire in questo ambito per digitalizzare completamente l’intera catena del valore aziendale: produzione, magazzino, canali di distribuzione, personale, fornitori, relazione con il cliente.
Raggiungere la massima integrazione di queste aree permette di beneficiare dell’ottimizzazione di tutti i processi, la riduzione di tutte le tipologie d’errore, l’efficientamento energetico degli stabilimenti, la maggiore flessibilità in ciascuna fase di lavorazione, la celerità e l’immediatezza del dato nel rapporto col cliente, che accompagnano altre innovazioni della rivoluzione industriale 4.0. Questa trasformazione comporta una nuova configurazione, orchestrazione e integrazione dei processi che vedono adottare soluzioni digitali su più piani: stampa 3D, robotica, cloud/fog/edge computing, IoT, cybersecurity, big data analytics. È però indispensabile che questi nuovi software si integrino perfettamente con software gestionali e operativi già in possesso, al fine di ottimizzare la gestione degli standard di produttività.
I benefici fiscali
La rilevanza della digitalizzazione per aumentare la competitività delle imprese italiane è stata recepita dal Governo, che ha incluso, a partire dalla legge di Bilancio 2017, gli incentivi riferiti al piano Industria 4.0 e ai successivi piani Impresa 4.0 e Transizione 4.0: iperammortamento al 140% per i software indicati nell’Allegato B della citata Legge di Bilancio acquistati nel 2018 e 2019, e credito d’imposta del 15% per quelli acquistati nel 2020.