IoT e simulazione dei processi industriali
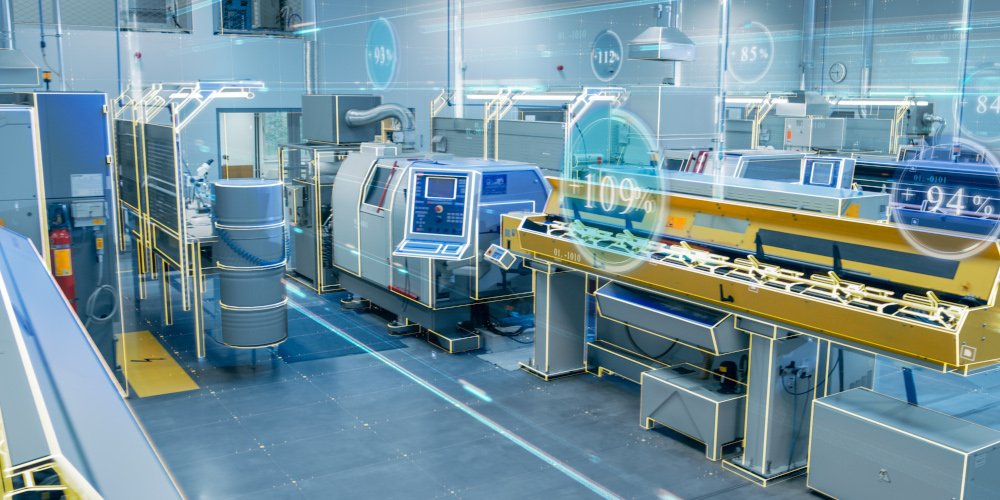
Ottimizzare un processo produttivo esistente o progettarne uno nuovo comporta investimenti tecnologici, costi operativi, organizzativi e per la formazione delle risorse umane. Dimostrare la fattibilità tecnica e quantificare il ritorno economico dell’investimento non è semplice in contesti caratterizzati da variabilità dei tempi di lavorazione, imprevedibilità degli eventi, come i guasti, condivisione delle risorse umane e tecnologiche.
La simulazione dinamica della produzione industriale permette invece di prevedere il funzionamento e di evidenziare in anticipo eventuali problemi, mediante la realizzazione di un modello matematico del processo da analizzare.
Simulazione dei processi produttivi
La simulazione del funzionamento dei processi produttivi e logistici non è un problema banale, poiché questi sistemi sono caratterizzati da elevata complessità, numerose interrelazioni tra i diversi processi, indisponibilità e stocasticità dei parametri dei sistemi. La simulazione, consentendo l’analisi della realtà con un elevato livello di dettaglio e padroneggiando la complessità del sistema, genera un gran numero di informazioni utili.
Per creare un modello di simulazione utile e funzionante è opportuno procedere con una serie di passi:
– definizione degli obiettivi e delle problematiche da esaminare;
– stesura di un modello concettuale;
– validazione del modello concettuale;
– analisi dei dati in ingresso;
– scrittura del modello in termini matematici;
– calibrazione e valutazione;
– definizione di un piano degli esperimenti;
– analisi dei dati in uscita.
Una volta costruito il modello, bisogna tradurlo in un programma su calcolatore. Per problemi di piccole dimensioni è possibile usare strumenti informatici di uso comune come gli spreadsheet (excel e simili) dotati di funzioni ‘what if’, ma nella maggior parte dei casi è necessario ricorrere a strumenti più potenti.
Linguaggi, applicazioni e modelli
Esistono alcuni linguaggi specializzati per la simulazione, quali SIMSCRIPT, MODSIM e GPSS, ma la soluzione utilizzata più comunemente nell’industria è quella di ricorrere alle piattaforme di modellazione: applicazioni di tipo interattivo per la simulazione a elementi discreti (DES), che racchiudono l’esperienza di modellazione dei processi operativi maturata negli ultimi 50 anni (i primi software di modellazione risalgono agli Anni ’70), come AutoMod, Simul8, Arena Simulation, Simio, AnyLogic, Witness, Micro Saint Sharp e ANSYS. Queste applicazioni sono dotate di potenti ambienti di sperimentazione, analisi, visualizzazione 2D e 3D, confronto e ottimizzazione di scenari alternativi per correlare con rapidità le informazioni e trasformarle con facilità in decisioni. Sono di utilizzo relativamente semplice e quindi molto adatte a costruire rapidamente modelli, anche sofisticati.
La maggior parte di questi sistemi, è ora in grado di supportare la realizzazione di digital twin delle macchine, degli impianti e dei processi simulati.
Simulazione e Internet of Things
L’avvento delle tecnologie Internet of Things ha reso la simulazione ancor più indispensabile per progettare i nuovi dispositivi e i nuovi processi industriali. I ‘connected devices’ stanno proliferando. Nascono continuamente prodotti innovativi e quelli esistenti beneficiano di funzionalità sempre più avanzate e smart. Secondo le stime degli analisti, entro il 2025 ci saranno oltre 70 miliardi di dispositivi connessi in tutto il mondo, con un valore di mercato dell’ordine dei 12.000 miliardi di dollari. Automazione industriale, smart city, elettronica di consumo e virtualmente tutti gli aspetti dell’economia globale saranno interessati dall’IoT. Ogni azienda sarà presto chiamata a implementare una strategia IoT per i propri prodotti e dovrà passare da ‘prodotti muti’ a “prodotti smart connessi” con nuove tecnologie innovative.
Il valore dell’IoT risiede principalmente nei dati trasmessi dagli oggetti e raccolti. Per esempio, le vibrazioni di una turbina, la temperatura di un motore o la velocità di un nastro trasportatore possono dare informazioni cruciali per migliorare le condizioni operative. Molti produttori hanno sviluppato piattaforme in grado di connettersi ai sistemi di simulazione per ottimizzare le performance e guidare le innovazioni future. Gli strumenti più utilizzati sono i digital twin: ogni oggetto fisico ha una copia virtuale, un gemello digitale. L’oggetto fisico (physical twin) e il modello digitale (digital twin) costituiscono un sistema ciberfisico (CPS, cyber physical system) in cui c’è un continuo scambio di dati tra oggetti fisici e modelli digitali contenuti nei simulatori. I dati raccolti dall’oggetto fisico e dall’ambiente tramite i sistemi IoT possono essere comparati e integrati con quelli della copia virtuale per identificare possibili problemi di performance, prevenire fermi per guasti (manutenzione predittiva) e condizioni anomale.
Dalla simulazione all’operational intelligence
Creare valore dai dati generati dai prodotti connessi è una delle ragioni principali per cui le aziende investono nell’IoT Industriale. La tecnologia di simulazione combinata con il machine learning può aiutare i progettisti a identificare e valorizzare i dati necessari per migliorare progetti e prestazioni e sviluppare prodotti di nuova generazione.
Con i sistemi simulativi è possibile simulare tutte le fasi di un processo produttivo, ridurre sprechi e tempi di produzione. Grazie all’utilizzo di sensori intelligenti, vengono rilevati in tempo reale i dati necessari per studiare e ottimizzare i processi produttivi, e intervenire preventivamente. Le tecniche di big data analytics permettono alle aziende di gestire questo volume di dati, di elaborarli e analizzarli al fine di renderli utilizzabili.
I risultati di queste analisi, in una realtà aziendale permettono l’ottimizzazione dei processi produttivi, la gestione innovativa dei flussi di lavoro e attività di operational intelligence indirizzate a una maggior capacità di interpretazione dei bisogni e delle necessità delle proprie infrastrutture.
Da un punto di vista strategico, permettono di avere una visione più precisa del mercato, della concorrenza e del comportamento dei clienti per adottare strategie mirate di customer experience.
Gli stessi dati possono fornire le basi per lo sviluppo delle successive generazioni di prodotti (simulation-driven product development). L’avvento dell’IoT ha reso la simulazione ancor più indispensabile per progettare i nuovi dispositivi, che si tratti di apparecchiature medicali, tecnologia wearable, auto connesse o turbine industriali.
I prodotti vengono sviluppati in un primo momento virtualmente utilizzando i simulatori congiuntamente agli strumenti di CAD e PLM e successivamente vengono materializzati grazie a modelli informatici, in grado di associare a ogni prodotto e a ogni azione del mondo fisico una rispettiva riproduzione fedele nel mondo virtuale.
Le fasi principali del processo di produzione basato sulla simulazione sono quattro.
1. Ideazione e modellazione del prodotto virtuale, attraverso l’uso di software.
2. Produzione virtuale che evidenzia tutte le componenti indispensabili o da modificare.
3. Produzione dell’oggetto fisico vero e proprio.
4. Operazioni di controllo che vengono eseguite sul prodotto al fine di migliorarlo.
Nell’era dell’Industria 4.0 le aziende devono accelerare la produzione, ridurre i tempi di consegna, migliorare velocità e flessibilità delle modifiche di progettazione e garantire la qualità del prodotto monitorando l’intero flusso di lavoro fino alla produzione. Grazie ai sistemi di simulazione è possibile predire eventuali problematiche, si ottengono prodotti di maggior qualità e si può riprogettare il prodotto prima che venga realizzato concretamente.
I vantaggi
I principali vantaggi che spingono le industrie a scegliere la simulazione integrata con IoT, intelligenza artificiale, big data e advanced analytics, sono:
– ottimizzare le performance;
– ridurre il time to market;
– ridurre le spese per i progetti e per i test sperimentali;
– ottenere maggior flessibilità e qualità dei prodotti;
– rendersi conto preventivamente di eventuali difetti e malfunzionamenti nella produzione.
La simulazione sta diventando una realtà nel settore industriale, non solo nelle grandi aziende, ma anche nelle piccole e medie imprese più innovative.
Industria 4.0, Internet of Things