A che punto siamo con Industria 4.0
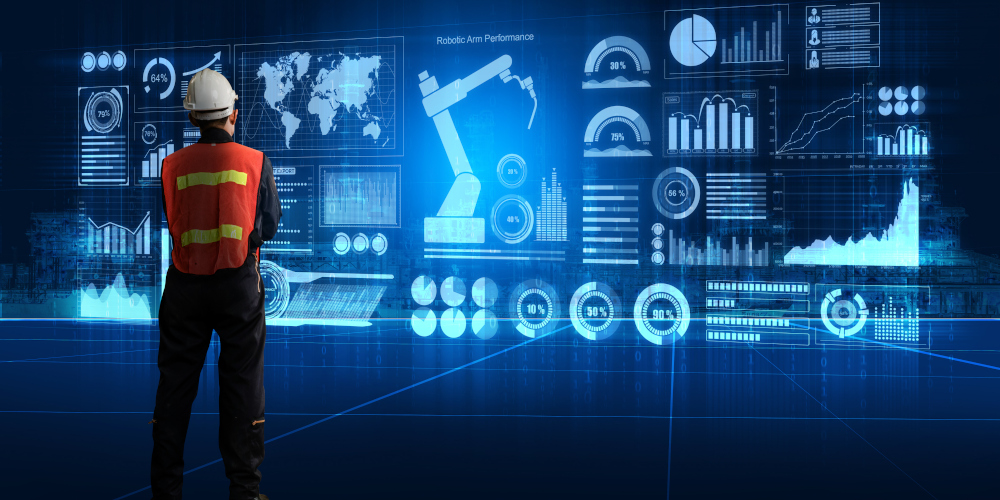
Le nuove tecnologie digitali che sempre più entrano negli ambienti di fabbrica avranno un impatto profondo nell’ambito di quattro direttrici di sviluppo. La prima riguarda l’utilizzo dei dati, la potenza di calcolo e la connettività, e si declina in big data, open data, Internet of Things, machine-to-machine e cloud computing per la centralizzazione delle informazioni e la loro conservazione.
La seconda è quella degli analytics: una volta raccolti i dati, bisogna ricavarne valore. Oggi pare che poco più del 4% dei dati raccolti viene utilizzato dalle imprese, che potrebbero invece ottenere vantaggi a partire dal ‘machine learning’, dalle macchine cioè che perfezionano la loro resa ‘imparando’ dai dati via via raccolti e analizzati. La terza direttrice di sviluppo è l’interazione tra uomo e macchina, che coinvolge le interfacce ‘touch’, sempre più diffuse, e la realtà aumentata.
Infine, c’è tutto il settore che si occupa del passaggio dal digitale al ‘reale’ e che comprende la manifattura additiva, la stampa 3D, la robotica, le comunicazioni, le interazioni machine-to-machine e le nuove tecnologie per immagazzinare e utilizzare l’energia in modo mirato, razionalizzando i costi e ottimizzando le prestazioni. Un passaggio epocale, insomma, per un Paese manifatturiero come il nostro, un’opportunità per le imprese che sapranno coglierla, ma anche il rischio di restare indietro per chi non avrà le risorse, soprattutto in termini di conoscenze, per cogliere il cambiamento. L’era della fabbrica connessa sta cambiando profondamente gli equilibri del mercato ed è destinata a delineare i nuovi campioni della competizione internazionale.
In questo scenario, Office Automation ha pensato fosse cosa utile organizzare due Tavole Rotonde a cui ha invitato a partecipare diversi fornitori protagonisti del mondi Industria 4.0, per tracciare lo stato dell’arta del tema ‘fabbrica connessa’ e quindi delineare gli sviluppi e i trend per l’immediato futuro. Ai due appuntamenti hanno aderito 19 realtà, che ringraziamo anche per l’ampio spettro di analisi emerso dalla discussione. A moderare le due tavole rotonde è stato Marcello Maggiora, collaboratore storico di Soiel e Direttore Divisione Tecnologica e Strategie Digitali della Fondazione Compagnia di San Paolo di Torino, che ha introdotto il tema fornendo una lucida analisi della situazione nel nostro Paese.
Marcello Maggiora, Direttore Divisione Tecnologica e Strategie Digitali della Fondazione Compagnia di San Paolo
Il contesto italiano è più difficile rispetto a quello di altri Paesi. Le tante realtà produttive del nostro Paese pensavano di risolvere tutto con il programma Industria 4.0, invece le cose non sono andate proprio così e ora c’è dell’affanno e la sindrome da novità ha acquistato peso. Anche perché da noi l’Università non sta dando quel sostegno che si sperimenta all’estero. Gli indici che misurano questa evoluzione segnalano l’Italia molto indietro, in particolare nella connettività, ma anche nella qualità dei prodotti, che magari costano meno ma poi devono essere sostituiti con l’avanzamento dei progetti. Le nostre industrie sono inoltre grandi utilizzatrici di device, spesso però ridondanti.
Bisognerà quindi lavorare molto su questi aspetti e non nutrirsi più di grandi attese e di false speranze. Un po’ più di cultura inoltre non guasterebbe. L’IT non ha saputo esercitare un ruolo trainante; preoccupandosi solamente della riduzione dei costi ha fallito nell’obiettivo di miglioramento innovativo dell’attività produttiva. L’innovazione buona invece ha i suoi costi e di questo si deve tenere più conto in futuro. La sola via che io vedo percorribile è quella di lavorare bene ed evitare progetti banali.
Un tema da non tralasciare è poi quello della cyber sicurezza che la maggiore connettività crea, anche in considerazione del fatto che molti software introdotti nell’industria anche nel recente passato sono datati, a volte anche di oltre vent’anni, con tutte le conseguenze immaginabili. Oggi anche il mondo produttivo non è più confinato tra quattro mura, mentre molti asset sono basati su protocolli facilmente aggredibili.
In generale occorre fare molte riflessioni e ricercare un nuovo equilibrio. L’Italia ha la capacità per farlo e anche in tempi ragionevoli. In quest’ottica l’esperienza universitaria dovrebbe essere sfruttata di più.
Paolo Aversa, Managing Director di ally Consulting
ally Consulting è una società di consulenza specializzata nell’IT che accompagna il cliente nel percorso di trasformazione digitale, rivolgendosi principalmente alle piccole e medie aziende del settore manifatturiero. Con una copertura a 360° delle esigenze della smart factory, operiamo nell’implementazione di sistemi gestionali ERP con un approccio flessibile, innovativo e concreto. Forte dell’esperienza trentennale maturata nell’IT, offriamo ai clienti un servizio di consulenza completo: analisi e re-engineering dei processi, scelta e implementazione delle soluzioni rivolgendoci principalmente al mercato manifatturiero di piccole e medie dimensioni.
In questo ambito la situazione italiana, relativamente ai progetti di Industria 4.0 e implementazione dei sistemi ERP, è allineata a quella che ritroviamo nei principali Paesi europei con cui lavoriamo.
Durante la pandemia abbiamo visto che la maggior parte dei progetti in corso è sostanzialmente andata avanti, mentre abbiamo riscontrato un freno negli investimenti in tecnologie e applicazioni che avrebbero migliorato i processi aziendali. Infatti si è preferito dirottare le spese verso tecnologie abilitanti la pratica dello smart working anche se ci si è concentrati molto poco sul diffondere all’interno delle proprie aziende un metodo di lavoro che potesse includere la partecipazione in remoto.
Tuttavia, da alcuni mesi notiamo un nuovo e crescente interesse, soprattutto in soluzioni rivolte alle aree della logistica, della produzione e alle tecnologie dell’ultimo miglio. Queste risorse vanno incanalate al meglio per migliorare la gestione e la produttività ed è qui che entriamo in gioco noi con le nostre competenze consulenziali di mappatura e analisi dei processi. Il nostro lavoro è focalizzato sull’ottimizzazione dei processi, con lo scopo primario di affiancare il cliente e facilitare l’adozione di tecnologie e soluzioni per rendere meno rigidi i processi stessi, contribuendo così a migliorare le performance del business.
Jacopo Cassina, Ceo & Founderb di Holonix
Holonix è nata nel 2010 dal Dipartimento di Ingegneria Gestionale del Politecnico di Milano dopo anni di consolidamento in progetti di ricerca nazionali e internazionali. La profonda integrazione tra le competenze necessarie nei progetti di ricerca con il know-how acquisito in 12 anni di collaborazione con le PMI del manufacturing italiano è il catalizzatore ideale per la creazione di prodotti e di servizi concreti dal Dna innovativo, in grado di adattarsi e crescere in base alle esigenze reali dei clienti, evolvendosi ulteriormente in nuovi progetti sulla base di esperienze sul campo e veicolando le scoperte della ricerca verso l’uso quotidiano. In Holonix ci occupiamo e abbiamo esperienza di entrambi i domini dell’IoT: sia il machine to machine, dove offre una soluzione per i produttori di macchinari industriali chiamata i-Live Machines sia la tracciabilità, usando RfId, BLE e altre soluzioni, dove, con la nostra i-Like Platform, realizziamo soluzioni custom.
Holonix è partner Ucimu, Ucina, associati Federmacchine e IBM Registered Business Partner.
Pur occupandoci di IT, le persone e il team sono per noi il cuore di ogni soluzione di successo e con questo intendo sia all’interno di Holonix, dove grazie ai progetti di innovazione abbiamo una formazione continua e la possibilità di venire a contatto con le idee, le menti e le soluzioni più innovative d’Europa, sia nella relazione con i nostri clienti, i cui operatori, grazie alle nostre soluzioni, hanno una nuova disponibilità di dati e di informazioni per prendere decisioni e con cui innescare processi di miglioramento continuo. Questo è per noi lo scopo ultimo dell’IoT ed è l’approccio che definiamo di ‘intelligenza aumentata’. Insieme ai prodotti software e ai progetti custom, accompagniamo le aziende durante il loro percorso di trasformazione digitale anche con momenti di formazione e continua collaborazione, incrementando le loro competenze inerenti le nuove tecnologie e supportando il loro avvicinamento al mondo IoT, attraverso percorsi mirati sulle specifiche necessità.
Per quanto riguarda l’Italia, siamo un po’ in ritardo rispetto ad altri Paesi europei nella adozione dell’Industria 4.0. Si è operato troppo spesso nella sola logica di una adozione mirata alla riduzione dei costi e i vendor non hanno saputo cavalcare al meglio questa opportunità, usando spesso un linguaggio sacerdotale che non ha giovato e ha contribuito ad accrescere lo scollamento tra attese e realizzazioni. Sono state fatte promesse esagerate, non alla portata delle PMI. Creando un clima di sfiducia, per fortuna non di disinteresse che è ritornato ora in auge.
Adesso, come stiamo vedendo anche noi, ci sono persone che sanno parlare fattivamente all’imprenditore usando il suo linguaggio. Cosa che dovrebbe far migliorare lo spirito collaborativo tra le parti e consentire alle soluzioni di Industria 4.0 una maggiore diffusione, uscendo dalla nicchia di eccellenze nelle quali sono rimaste di fatto fino a oggi.
Guido Colombo, Presidente & Ceo di Orchestra
Orchestra, azienda nata nel 2016 come spin off del Politecnico di Torino, ha posto fin dall’inizio al centro del suo business un concetto di Industria 4.0 in cui l’interconnessione delle macchine non è il fine del progetto, bensì il punto di partenza per offrire servizi digitali volti ad accrescere la competitività delle imprese, in particolare piccole e medie. Per fare questo ci avvaliamo di una architettura Industrial IoT che coniuga l’edge computing con il cloud: Cloud Driven Edge Computing. Questo approccio consente di mettere a disposizione nuovi servizi digitali bordo macchina che sfruttano algoritmi di intelligenza artificiale e forniscono funzioni di supporto allo sviluppo di applicazioni di realtà aumentata. Si tratta di servizi a valore aggiunto capaci di dare supporto attivo agli operatori di produzione e ai manutentori degli asset produttivi. Un grande aiuto può arrivare in particolare ai responsabili di reparto che necessitano di nuovi servizi digitali real time rispetto ai cicli macchina per anticipare eventuali derive di processo, per guidare le giovani maestranze nell’attrezzaggio e nella configurazione più opportuna delle macchine in funzione del prodotto in lavorazione, per offrire funzionalità diagnostiche ai manutentori e suggerire ai responsabili operazioni correttive per i processi produttivi in corso. Sul versante della fabbrica, il nuovo SMARTEdge Next Generation, frutto dell’attività di R&D di Orchestra e in fase di rilascio da pochi mesi, supporta questa nuova generazione di servizi digitali. Sul versante, invece, della gestione dei processi produttivi, la società mette a disposizione dei clienti di piccole dimensioni il suo MiniMES, una Web App utilizzabile da qualsiasi pc o device mobile per pianificare, avanzare, tracciare e controllare la produzione in tempo reale. Abbiamo racchiuso tutto questo in una suite di prodotto che abbiamo denominato Retuner per alludere alla nostra mission di riaccordare le Pmi manifatturiere sullo spartito di Industria 4.0. L’80% dei nostri clienti, che ci ha ingaggiato per la prima nuova macchina, ci ha poi fatto interconnettere l’intero parco macchine e ha incominciato a usare le soluzioni software da noi proposte. La nostra Ricerca e Sviluppo sta dando quindi i frutti sperati e il livello di innovazione raggiunto ci permette di contraddistinguerci sul mercato. Il sistema Retuner offre così un supporto attivo a tutti i processi del manifatturiero, per avere macchine che comunicano in modo intelligente con l’uomo, che rimane al centro del sistema produttivo con un cambio di ruolo e attitudini per un nuovo coinvolgimento e una crescita professionale.
Gabriele Montelisciani, Ceo di Zerynth
Una piattaforma IoT per aiutare le imprese del manifatturiero a spingere su innovazione e sostenibilità trasformando presse, torni e telai in impianti 4.0: è l’obiettivo di Zerynth, startup fondata nel 2015, che vuole aiutare aziende manifatturiere e system integrator a trarre valore dai dati e aprirsi all’efficientamento di prodotti e processi e al risparmio energetico. In tutti i settori industriali, dall’automotive alla refrigerazione industriale, dallo smaltimento dei rifiuti alla nautica fino all’agricoltura. L’azienda ha come socio il fondo Vertis Venture 3 Technology Transfer che ha investito due milioni di euro, acquisendo il 36% della società. Il tema della connettività lo approcciamo in due modi complementari. Innanzitutto, fornendo le informazioni direttamente dalla macchina per mettere in condizione l’imprenditore di prendere delle decisioni di ottimizzazione ed efficientamento nel modo più consapevole possibile. Un esempio, nel settore delle materie plastiche, è il lavoro fatto con Armal. Abbiamo sviluppato un sistema IoT industriale per il monitoraggio in tempo reale del consumo energetico delle presse che ha consentito di ridurre i consumi energetici mediamente del 40%, con picchi fino al 70%. Oppure, nel settore dello smaltimento dei rifiuti, dove non esisteva un sistema che, con tecnologia molto semplice ma molto efficace, potesse dare in tempo reale le informazioni sui livelli del percolato all’interno della discarica. E tutto questo senza cambiare le macchine, che è il secondo elemento del nostro approccio. Proponiamo soluzioni semplici e facilmente adattabili, nella logica del plug & play, avvalendoci di partner specializzati nei sistemi ERP e MES, con percorsi di innovazione anche già in corso. L’Italia è abbastanza allineata con il resto d’Europa nella corsa alla Industria 4.0, ha solo bisogno di maggiore consapevolezza e cultura manageriale, utili per un cambiamento epocale come questo.
L’obiettivo che ci siamo dati, mentre ci avviamo a chiudere il 2022 con un fatturato in forte crescita rispetto al milione di ricavidello scorso anno, è superare la logica dell’azione mirata a ottenere semplicemente un supporto economico con gli incentivi 4.0 per l’acquisto di nuove macchine. Preferiamo piuttosto fare riferimento al Pnrr che dà una visione più ampia, di filiera e di controllo dell’intero processo, per investire sulle aziende che cercano soluzioni concrete in tecnologie per rendere più efficienti le loro produzioni.
Andrea Robbiani, Sales Manager di Corvina-Exor
Corvina, società del gruppo Exor International, è una start up nata nel 2021 che offre soluzioni di servitizzazione e digitalizzazione della supply chain, attraverso una piattaforma di cloud industriale, grazie alla quale abilitiamo la raccolta dei dati, che provenegono dai sistemi produttivi e dai sistemi applicativi aziendali, oltre a lavorare sui processi industriali al fine di ottimizzarli in un’ottica ‘lean manufacturing’.
La piattaforma Corvina Cloud, abilita processi di machine learning e artificial intelligence avanzati, per consentire alle aziende di vedere oltre, essere innovative e più veloci nel rispondere alle mutevoli esigenze del mercato. La caratteristica di Corvina è quella di supportare la trasformazione digitale della filiera produttiva, indipendentemente si abbia a che fare con macchinari moderni o datati, armonizzando protocolli industriali diversi, fornendo un layer di comunicazione cloud-edge, che permette la correlazione strutturata dei dati, al fine di soddisfare le molteplici ‘funzioni obiettivo’ di produzione, quali per esempio, la manutenzione predittiva, il monitoraggio e l’aggiornamento remoto dei macchinari, l’azzeramento degli scarti di produzione, il monitoraggio dei costi energetici.
La nostra soluzione aiuta il mondo manufatturiero a intraprendere il percorso della digitalizzazione su tutta la supply chain, in modo relativamente agile, ricorrendo a metodologie consolidate, allo scopo di ottimizzare i processi produttivi, riducendo sprechi e inefficienze. Per raggiungere questi obiettivi molto sfidanti, il team di Corvina opera in sinergia con i clienti affinchè vi sia una chiara percezione dei cambiamenti non solo tecnologici, ma anche culturali, dimostrando che si può innovare, senza stravolgere il DNA della azienda. Ai nostri clienti forniamo elementi chiari e precisi sugli investimenti necessari, sui tempi di realizzazione, supportando altresì anche tutto il processo di formazione degli operatori.
Ciò che Corvina porta in dote ai propri clienti, si basa sulla decennale esperienza di Exor International, che da circa due anni ha realizzato a Verona, una vera e propria smart factory, nella quale si producono sistemi elettronici industriali, dedicati principalmente al mondo dei produttori di macchinari industriali. Nella smart factory sono presenti tutte le tecnologie abilitanti la digitalizzazione dei processi produttivi e di gestione del personale. È possibile visitarla per rendersi conto di ciò che si può realizzare.
L’imprenditore vuole soprattutto comprendere e misurare il vantaggio competitivo, i tempi e i costi di realizzazione, che devono necessariamente essere certi, avendo come obiettivo la realizzazione di un progetto condiviso e non vincolato a un particolare fornitore o a uno specifico prodotto.
Concludendo, preme sottolineare come per portare a compimento con successo la trasformazione digitale, è essenziale la chiarezza di obiettivi, per evitare di digitalizzare ciò che non serve, quindi anche gli sprechi. Circa il 30% delle iniziative di digitalizzazione subiscono bruschi rallentamenti, se non addirittura lo stop, proprio per mancanza di chiarezza di intenti o peggio, per l’adozione di soluzioni tecnologiche standard, che mal si sposano in contesti produttivi che necessitano di soluzioni ‘custom by design’.
Pier Luigi Zenevre, Director BU Industry 4.0 di Alleantia
Alleantia è una software house che esiste dal 2011, nata da una idea del suo fondatore Stefano Linari, per realizzare dispositivi e una piattaforma di IoT integration per impieghi industriali all’insegna dell’innovazione e dell’integrazione sempre più performante fra il mondo OT e quello delle applicazioni IT a valore. Questo anche grazie alla strategia di business Alleantia che fa leva sulle collaborazioni industriali con i più importanti partner globali fornitori di tecnologie IT, sistemi hardware e software.
Più in particolare le soluzioni software ‘Connected by Alleantia’, installate negli IoT edge gateway di primari costruttori, integrano ogni tipo di macchina, impianto produttivo, bene strumentale di trasporto e dispositivo di automazione industriale con il web, i sistemi aziendali e le nuove applicazioni IT preesistenti o di nuova concezione con interfacce ‘pronte all’uso’.
La disponibilità di dati IoT, liberati da Alleantia, abilita l’ecosistema di partner “Connected by Alleantia”, sviluppatori di applicazioni software, system integrator e le nuove piattaforme IoT, ad implementare innovative soluzioni 4.0 focalizzate nella creazione di nuovo valore, di nuovi modelli di business e nelle nuove opportunità per la crescita delle nuove competenze professionali. In questo modo si permette a ogni azienda di realizzare la propria ‘Industrial Internet of Things plug&play’.
Nell’attuale contesto produttivo si assiste a un coacervo di situazioni e sistemi che, per una significativa parte di utilizzatori finali, lasciano trasparire la mancanza al loro interno di una regia che concepisca, gestisca e coordini i progetti di trasformazione e di innovazione digitale in corso per portarli a compimento con pieno successo. Si può tranquillamente parlare di mancanza di cultura d’impresa nel pensare e gestire l’innovazione legata ai processi di trasformazione digitale nell’industria. Le ridotte dimensioni delle nostre imprese e la scarsa disponibilità di competenze tecniche sono le ulteriori cause e i motivi che spiegano questa situazione confusa. In Germania, dove le dimensioni d’impresa sono maggiori, la situazione è diversa e le piccole realtà, tipicamente corrispondenti alle nostre medie imprese, sono spesso al traino di quelle maggiori che fanno da battistrada grazie alla più forte dotazione di risorse umane specializzate nei vari domini applicativi 4.0 e capacità di budget d’investimento.
Il fermento è però tanto anche nel nostro Paese e non mancano iniziative di eccellenza nel campo dello smart manufacturing.
In questo senso la pandemia ci ha aiutato, contribuendo al lancio di parecchi progetti di trasformazione digitale gestiti con maggiore efficacia grazie alla capacità delle nostre tecnologie di condurre l’implementazione e i test di funzionamento con modalità operative in remoto. Sono quindi emerse delle opportunità, prima dormienti, che sono state sviluppate con minori rischi di implementazione per effetto di tempi e costi decisamente più contenuti, nonché di un monitoraggio dei progetti più puntuale e finalizzato all’immediata identificazione della loro rispondenza ai piani di deployment o degli scostamenti rispetti agli obiettivi predefiniti.
Servirebbero delle spinte. In prima battuta un investimento del sistema Paese nella creazione di filiere di ecosistemi di aziende e di tecnologie disponibili per la corretta realizzazione di progetti di trasformazione digitale in considerazione della loro sempre più ampia trasversalità e della sempre più crescente complessità/integrazione, come ha fatto e sta facendo la Germania. Poi è auspicabile una politica che dia maggiore visibilità e possibilità di collaborazione realmente aperta a una platea di vendor e utilizzatori globali di tecnologie 4.0 alle tante aziende che in Italia sviluppano del software soluzioni 4.0 eccellente e di qualità internazionale. Da accompagnare con azioni di consapevolezza e di creazione della cultura sull’importanza della disponibilità dei dati e della loro sovranità, spesso sottovalutata.
Creare valore da un utilizzo migliore più efficace, con opportune regole, dei dati IoT condivisi anche grazie al supporto dei necessari strumenti di cybersecurity, con ritorni degli investimenti che si concretizzano nel giro di pochi mesi, è uno degli obiettivi che ci siamo prefissi come Alleantia.
Antonio Sandri, Direttore Commerciale di Sorma
Sorma nasce nel 1980 come società di consulenza con lo scopo di coniugare due anime, quella organizzativa e quella informatica, nell’ambito di un unico progetto aziendale. Con questo obiettivo sviluppa e implementa Si5, un sistema ERP ad alto contenuto organizzativo in grado di garantire un effettivo vantaggio competitivo ai clienti aiutando l’impresa a migliorare i processi gestionali e l’organizzazione supportando, contemporaneamente, sia la gestione operativa che le decisioni strategiche. L’elemento che contraddistingue la proposta di Sorma è l’impegno alla soluzione dei problemi concreti del cliente, con una soluzione applicativa di alta qualità, implementata con la massima attenzione al contributo organizzativo verso l’efficienza, nel rispetto delle particolarità di ogni realtà aziendale. Sorma si caratterizza, inoltre, per l’impiego di una metodologia operativa in grado di assicurare interventi mirati sulle reali problematiche aziendali, permettendo di vestire con un abito su misura l’impresa del cliente, pur salvaguardando l’integrità e la coerenza del prodotto standard.
In questo contesto le criticità che incontriamo sono tante. In cima metterei la corsa tra gli attori dell’offerta per aggiudicarsi le commesse, spesso con proposte improvvisate o quanto meno non adeguatamente soppesate, che finiscono per disorientare l’utenza e creare sfiducia. Nella produzione manca spesso una figura in grado di dialogare in modo competente sulle innovazioni che si vanno a proporre. La norma è quella di scegliere come responsabile di progetto il collaboratore aziendale più skillato.
Ma le aziende devono farsi ‘consigliare’ per raggiungere obiettivi tangibili e migliorare, efficientando, i processi interni. I tempi sono diversi, ci vogliono oggi figure molto skillate, in grado, tra l’altro, di analizzare i dati, oltre il solito foglio Excel.
Ormai in Italia di grandi industrie non ce ne sono quasi più, il bacino produttivo è formato da piccole e medie aziende. In queste realtà, per esempio, perché il MES sia realmente produttivo va implementato concretamente. Le sfide sono tante e lo Stato dovrebbe intervenire in due modi per facilitare l’adozione di iniziative Industry 4.0: sotto forma di agevolazioni e semplificando gli iter burocratici.
Il ricorso alla consulenza qualificata, è il suggerimento di questo manager alle aziende, è una prassi utile prima di imbarcarsi in investimenti tecnologici, in grado di impattare in modo rilevante l’attività produttiva nei prossimi anni, per non dire decenni.
Felice Petrignano, Advisory Senior Partner Technical Specialist, IBM Sustainability Software
L’esperienza di IBM con i clienti e i risultati della IBM CEO Survey 2022 portano ad affermare che l’Italia si posiziona un po’ in ritardo nel percorso verso l’Industria 4.0, percorso che a livello internazionale è invece sempre più veloce. Alcuni numeri: il 45% dei CEO intervistati in Italia rispondono che la loro priorità principale è il miglioramento dell’agilità e flessibilità operazionale, dato inferiore del 13% rispetto al dato internazionale; solo il 14% dei CEO Italiani si sentono fiduciosi nella loro capacità di gestire i maggiori rischi di business, contro il 37% degli altri Paesi. Infine, il 59% dei CEO Italiani si aspettano una crescente difficoltà nella conservazione delle competenze, un dato peggiore del 88% rispetto al dato globale. Nel nostro Paese abbiamo maturato importanti progetti in ambito Industry 4.0 sia con le grandi aziende sia con le PMI, anche grazie alla collaborazione con un ampio ecosistema di partner in grado di localizzare e adattare le soluzioni globali alle esigenze delle imprese sul nostro territorio. Per meglio sederci al fianco delle nostre PMI gli IBM Studios nel centro di Milano permettono di vedere e sperimentare le soluzioni in modalità agile, grazie alla metodologia ‘Garage’. IBM ha anche una significativa collaborazione con il Made del Politecnico di Milano dove le imprese possono vedere in azione casi d’uso di Industry 4.0, dalla manutenzione intelligente al controllo di qualità basato sul riconoscimento di immagini con AI.
Il ruolo delle nuove tecnologie è fondamentale per evitare sprechi nelle catene del valore. IBM ritiene che investire su digitale, intelligenza artificiale, cloud ibrido, sicurezza e automazione consenta di risolvere quelle inefficienze che poi condizionano i costi che sempre di più si ribaltano sul consumatore finale e dunque sui mercati. Riteniamo che questo sia il percorso corretto e che si debba continuare a insistere, anche facendo leva su nuovi fattori che agevolano gli investimenti. Dal nostro punto di vista: nuove soluzioni, competenze ed ecosistemi di partner locali e capacità di collaborazione con le PMI e una strategia per tradurre l’opportunità del PNRR in vantaggi competitivi durevoli.
La prima ondata IoT si è bloccata quando gli operatori hanno visto che il 99% dei dati raccolti non era usato. IBM integra i dati provenienti dai sensori di molteplici fornitori per alimentare soluzioni avanzate a supporto dei processi industriali. IBM sta collaborando con alcuni leader internazionali e grandi aziende italiane per rendere possibili nuovi livelli di agilità nelle operazioni con piattaforme intelligenti di gestione asset, edifici, supply chain, rischio climatico. Il sistema di monitoraggio di IBM riceve i dati dal campo provenienti da sensori, da contatori, da immagini video. Il sistema include modelli AI predisposti per l’industria e adattati in fase progettuale all’azienda. I risultati registrati su un ampio campione di clienti nel mondo vede una riduzione dei costi operativi dal 15% al 50%, un incremento della continuità dei processi produttivi del 10-20%; una riduzione significativa del turnover delle competenze.
Franco Andrighetti, Presidente & Ceo di EFA Automazione-Relatech
EFA Automazione, azienda che di recente è entrata a far parte del Gruppo Relatech, da oltre 30 anni si occupa di connettività, riuscendo con successo, anche in ambienti estremamente eterogenei, a far dialogare tra loro dispositivi e macchine e a confermarsi così un pioniere del paradigma dell’industry 4.0, che vede nella disponibilità dei dati uno dei suoi fondamenti.
La profonda conoscenza dei protocolli e dei driver di comunicazione, oltre alla naturale capacità di gestire i dati di processo del mondo dell’OT, ci rende gli interlocutori ideali per i tecnici del mondo IT che devono interfacciare le loro soluzioni con il mondo della produzione. Grazie alle nostre tecnologie e alla nostra expertise, gli operatori IT possono disporre in modo semplice e sicuro dei dati di processo, che normalizzati nei formati a loro più consoni, diventano immediatamente fruibili e, quindi, fattori chiave per implementare la vera integrazione digitale e supportare un corretto processo decisionale a tutti i livelli aziendali.
EFA Automazione grazie a un esteso portafoglio di prodotti, soluzioni e alla propria capacità di servizio è un vero e proprio facilitatore dell’interscambio di informazioni fruibili tra i due mondi IT/OT, elemento imprescindibile per la realizzazione di progetti o modelli di trasformazione digitale.
Per propria cultura e competenza l’approccio che EFA Automazione suggerisce alle aziende che vogliono approcciare la digital transformation è certamente bottom up. Esattamente come quando si costruisce una grande opera infrastrutturale la massima attenzione va posta alla posa delle fondamenta sulle quali edificare. Così, anche nei progetti di trasformazione digitale, il reperimento e la raccolta dei dati rappresenta un fattore di primaria importanza. Tuttavia, il dato, o ancor di più le montagne di dati grezzi, i cosiddetti ‘data lake’ che risiedono nel cloud, non hanno valore se non portano con sé una serie di caratteristiche genetiche sulla loro origine. La qualità, la veridicità, la sicurezza e la contestualizzazione del dato sono alcuni dei requisiti per garantire il successo di ogni progetto digitale che, a sua volta, si inquadra in un piano di evoluzione più ampio e a lungo termine.
Non si può quindi affrontare un percorso di digital transformation senza prima averne definito la strategia sulla base di una fotografia della realtà aziendale.
All’interno delle aziende la digitalizzazione è già presente, tuttavia, siamo ancora lontani dall’avere la corretta consapevolezza di come poterla sfruttare al meglio e quindi dal disporre della capacità essenziale di integrare le singole ‘conquiste digital’ all’interno di un percorso ben definito e a lungo termine. Ciò ci riporta al dato e al suo valore in quanto portatore di informazioni fruibili all’interno dei processi aziendali, che dovrebbero essere perfettamente organizzati e integrati tra loro. Il nostro mantra recita così: “Siamo un vettore tecnologico in grado di aiutare le aziende a definire il proprio percorso e accompagnarle lungo la strada di una digitalizzazione compiuta e, lo facciamo, grazie alla nostra capacità di estrapolare il massimo valore dai dati che le macchine generano costantemente ogni giorno, ogni ora, ogni secondo”.
Giacomo Coppi, Head of Digital Supply and Manufacturing, Italia e Grecia di SAP
SAP sta sempre più lavorando su una visione di ‘Business Process as a Service’, spostandosi dal modello applicativo verticale al processo end-to-end.
La sfida consiste nel rendere omogeneo e strutturato il processo che attraversa applicazioni diverse, per esempio ottenendo dati fruibili e omogenei dai modelli di dati specifici di tutte le applicazioni coinvolte, armonizzando le informazioni alla luce della crescente necessità di integrare dati di natura diversa, garantendo che il processo distribuito possa risolvere problemi computazionali di prossimità.
Da qui deriva la visione dell’edge come un ‘piccolo cloud’ da integrare nel processo di business. L’edge diventa un oggetto intelligente che esegue una parte del processo end-to-end in totale sinergia con il cloud e i diversi domini applicativi. Può eseguire compiti che in una logica cloud non sarebbe possibile per limiti tecnici, per esempio l’analisi ad alta frequenza di segnali di campo, e di generare solo eventi rilevanti per il processo stesso, penso agli eventi di manutenzione, sino all’applicazione di soluzioni innovative, come la manutenzione predittiva.
L’edge ha come effetto quello integrare sempre di più il campo, inteso sia come persone che strumenti, macchinari o altro, nel processo end-to-end, facendo sì che le azioni e i cambiamenti attivi o passivi fatti in qualsiasi punto del processo abbiano un effetto diretto e immediato sul comportamento del processo stesso, rendendolo più agile ed efficiente.
Come uno dei leader di mercato nelle applicazioni software per il business, SAP offre avanzate soluzioni in cloud per il mondo manufacturing che aiutano i clienti a sfruttare le nuove tecnologie (IIOT, AI, Edge) per connettere macchinari, persone e operazioni attraverso una supply chain digitale estesa, e integrare direttamente la produzione con le operation. Queste soluzioni non solo alimentano fabbriche intelligenti e altamente efficienti, ma forniscono la visibilità e la trasparenza necessarie per ridurre le emissioni e rispettare le nuove normative.
David Nalin, Responsabile Commerciale di Atomos Hyla (Gruppo Sedapta)
Atomos Hyla, azienda del Gruppo sedApta, è una società che racchiude esperienze e competenze nella fornitura di servizi di consulenza end-to-end e soluzioni tecnologiche integrate, volte a migliorare la produttività e l’efficienza nei settori manufacturing operations, sales & operation planning, automation e integrazioni con ambienti SAP, nel contesto Industry 4.0. Con sedi operative a Genova, Savona, Torino, Napoli, Milano, Bologna, Vicenza e Mantova, il team di Atomos Hyla, con pluriennale esperienza e consolidate competenze, offre soluzioni per tutte le aziende produttive, affiancandole a partire dalle analisi di affidabilità, collaborando con loro nella gestione delle soluzioni, in grado di orchestrare persone, processi e tecnologie aziendali.
Siamo convinti che quando la logistica, la struttura commerciale, la produzione e gli acquisti, lavorano insieme e in modo orchestrato, le aziende riescono ad affrontare al meglio le sfide del quotidiano. Per questo motivo la suite sedApta ha come obiettivo quello di colmare il divario fra pianificazione ed esecuzione della supply chain, favorendo la collaborazione tra reparti e attori dell’intera filiera, orchestrando processi e decisioni, simulando scenari e proposte. Ci contraddistinguiamo nell’aiutare le aziende a migliorare l’efficienza delle attività logistico-produttive e a implementare processi efficienti, collaborativi, orchestrati e misurabili, il tutto con una tecnologia moderna e costantemente ‘up to date’.
In ambito Industria 4.0, il nostro impegno è quello di offrire ai nostri clienti l’accesso alla tecnologia più affidabile e all’avanguardia disponibile. Siamo un’azienda italiana, orgogliosa di supportare le aziende del nostro territorio, in continua crescita anche oltre confine: infatti, siamo presenti all’estero in Francia, UK, Germania e Brasile.
Il PNRR sta dando un forte contributo, con i fondi spesi e programmati al sistema produttivo italiano, che ha compreso come sfruttare questa opportunità unica, soprattutto negli ambiti relativi all’innovazione e alla produttività.
Dal nostro osservatorio, gli ostacoli che vediamo alla piena adozione di agende digitali in ambito supply chain & manufacturing sono diversi, ma riteniamo che il primo problema da affrontare in questo momento sia e rimanga relativo alle competenze e al personale. Per togliere il freno a mano alla crescita, servono competenze in grado di sfruttare al meglio le soluzioni che sono messe a disposizione delle organizzazioni: la convergenza fra IT e OT, l’utilizzo di tecnologie ‘esplosive’ come AI e il digital twin, sono solo alcune delle sfide da cogliere nei prossimi anni per garantirsi un vantaggio competitivo per il prossimo decennio.
Matteo Orlandelli, Country Director Italy di CoreTigo
CoreTigo è una start up israeliana che mira a liberarsi dal cablaggio industriale fornendo soluzioni di comunicazione wireless IO-Link ad alte prestazioni per costruttori di macchine, integratori di sistemi e produttori di apparecchiature industriali. I nostri prodotti consentono la progettazione e il retrofit di macchine e linee di produzione in modo del tutto innovativo. La nostra soluzione senza fili deterministica permette di ottenere una comunicazione industriale con la stessa affidabilità della connessione via cavo aumentando così la flessibilità, l’adattabilità e la modularità del sistema.
Conseguenze naturali saranno poi la riduzione dei tempi di fermo, dei costi e un aumento della produttività. La nostra tecnologia, recepita tra l’altro dallo standard globale IO-Link Wireless, pur essendo studiata per tutte le applicazioni in movimento o rotazione , fornisce in realtà un vantaggio concreto in tutte le applicazioni che operano in ambienti industriali difficili. Insomma, possiamo dire che ci siamo inventati la prima trasmissione senza fili deterministica in ambito industriale.
L’ostacolo maggiore alla sua diffusione è rappresentato dalla mancata conoscenza di questa tecnologia e dalla paura generata dall’utilizzo in precedenza di tecnologie senza fili come il wi-fi e il bluetooth. Questo fenomeno è più diffuso soprattutto nelle piccole e medie aziende mentre nelle grandi la situazione per nostra fortuna è diversa. La pandemia ha dato una mano, così come a tutta la tematica dell’Industria 4.0, che sta finalmente incontrando il favore delle industrie secondo logiche inizialmente non comprese appieno.
Quello attuale è quindi un momento da sfruttare sotto tutti gli aspetti in ambito di digitalizzazione IIoT, e Industria 4.0 a maggior ragione ora che si può finalmente contare su di supporto wireless veramente affidabile. Il nostro target preferenziale sono le aziende da 100 a 500 dipendenti.
Tatiana Nevstrueva, Marketing & Business Development di Itworks
Itworks è una società di ingegneria di Ancona che sviluppa progetti di raccolta e integrazione dati in produzione, soprattutto per le aziende di trasformazione alimentare. Siamo da diversi anni fornitore di realtà come Gruppo Bauli, Galbusera, Tre Marie, Quality Food Group, Bouvard Italia che supportiamo nei progetti di controllo del prodotto e del processo, tracciabilità e digitalizzazione dei flussi, anche in ottica di Industria 4.0. Oltre al mondo food abbiamo realizzato progetti di MES avanzato nel settore di imballi alimentari, nello snodo produzione/logistica per grandi realtà oil&gas e nelle aziende farmaceutiche/nutriceutiche automatizzando controlli di processo specifici. Possiamo confermare che la pandemia ha cambiato radicalmente il modo di lavorare come noto. Non abbiamo però notato che la pandemia abbia velocizzato o rallentato l’implementazione delle tecnologie legate all’Industria 4.0 nelle aziende medio-grandi con le quali collaboriamo. Quelle aziende che avevano già pianificato investimenti e quindi allocato le risorse e messo in atto i progetti di Industria 4.0 sono andate avanti con l’implementazione, anche perché si tratta di investimenti con una durata pluriennale che vengono programmati molto in anticipo.
Rispetto alla prima ondata dei progetti nell’ambito di Industria 4.0 dove il driver principale dell’adozione delle nuove tecnologie era spesso il fattore economico, valutiamo che oggi il mercato si concentra di più sull’effettivo valore dei dati di processo che è diventato possibile raccogliere grazie all’interconnessione di fabbrica. Nell’ultimo periodo abbiamo ricevuto sempre più richieste di poter rendere fruibili i dati a disposizione con l’obiettivo di avere un’analisi, predittiva o descrittiva, volta a determinare i fattori di miglioramento del processo. Purtroppo, nonostante tutto ciò sono ancora poche le aziende italiane arrivate alla vera maturità rispetto agli obiettivi promossi dall’Industria 4.0, secondo i quali il dato collezionato deve essere analizzato per migliorare i processi. Possiamo parlare quindi della fabbrica ormai connessa al 90% che però non sta ancora sfruttando pienamente il potenziale del dato collezionato e a livello di campo e MES. A oggi, grandi applicazioni di cloud/big data/AI non si vedono ancora all’orizzonte.
La filosofia nel proporre le proprie soluzioni di Industria 4.0 è dimostrare ai clienti come l’analisi dei dati raccolti in azienda possa aiutare a ottimizzare il processo. Moltissime realtà sono ancora veicolate al ragionamento secondo il quale ‘ottimizzare’ vuol dire acquistare un macchinario più veloce, mentre è possibile spesso ottenere dei vantaggi con un investimento molto più contenuto valorizzando i dati già presenti in azienda.
Fabio Zucchini, Service & Revamping Manager di Lcs Group
Il Gruppo Lcs opera dal 1989 sul mercato italiano ed europeo come system integrator, offrendo soluzioni hardware e software complete, integrate e all’avanguardia per logistica interna, aeroporti e automazione industriale. In particolare l’attività di questo gruppo comprende: progettazione e fornitura di sistemi di movimentazione e stoccaggio automatici con project management accurato, magazzini automatici con trasloelevatori e miniload, soluzioni con shuttle, master-shuttle e satellite, moduli software proprietari per magazzini automatici, gestione della produzione e material handling, warehouse management system, warehouse control system, Scada, PLC, ammodernamento di impianti di automazione industriale e di material handling automatici esistenti indipendentemente dal costruttore, revamping assistenza e manutenzione, servizio remoto 24/7. Il nostro obiettivo è integrare l’eccellenza, ponendoci come partner del cliente per ottenere in ogni singolo progetto la soluzione più innovativa, affidabile e adatta alle esigenze analizzate e condivise, restituendo il massimo valore aggiunto. Lo sviluppo dell’e-commerce ha contribuito allo sviluppo di queste attività e quindi alla crescita del gruppo.
È necessario dare più spazio nelle industrie anche alla teleassistenza, perché anche il più piccolo dei sensori deve operare in rete, in quanto anche il suo ruolo è importante nell’ecosistema produttivo complessivo. La pandemia ha dato una spinta alla realizzazione di magazzini automatici e ha scompigliato le carte, favorendo le aziende più lungimiranti. Noi abbiamo sempre fatto Industria 4.0, anche sotto forma di analisi delle problematiche del cliente, evidenziando anche quanto sia importante una buona gestione dei dati.
Marco Crasnish, Ceo di Overlog
Overlog è un’azienda specializzata nella realizzazione di soluzioni software per la gestione logistica. L’insieme di prodotti che compongono la sua suite software garantisce soluzioni semplici ed efficaci che soddisfano ogni esigenza logistica aziendale. Grazie alla sua esperienza pluriennale, Overlog è in grado di offrire soluzioni ICT, software per la gestione logistica, prodotti hardware per ogni necessità e consulenze operative nell’ambito dei processi logistici. Con Industria 4.0 stiamo entrando nel vivo della sfida anche se molte aziende sono ancora perplesse o per lo meno non hanno ancora le idee chiare. A ogni modo in questi ultimi anni le aziende Italiane hanno avuto lo stimolo e la possibilità di interrogarsi sulle nuove opportunità tecnologiche e in alcuni casi di confrontarsi con esse. Questo secondo noi è sicuramente positivo, ma è fondamentale calare l’approccio tecnologico in una contestuale riprogettazione dei processi operativi. Non dobbiamo mai dimenticare che la tecnologia è uno strumento e non può essere il fine dell’investimento. Alcune recenti tecnologie sono oggettivamente molto interessanti, ma riteniamo ci sia ancora molto da fare per ‘scaricare a terra’ tutte le potenzialità che potrebbero fornire. Mi riferisco appunto a un approccio diverso ai processi, alla formazione del personale e all’utilizzo dei dati messi a disposizione e che troppo spesso vengono sottovalutati. I nostri interventi sono finalizzati a migliorare le performance del cliente e per farlo puntiamo a un approccio integrato, che può partire da una consulenza operativa, e sfrutta e integra tecnologie e sistemi per ottenere la soluzione più adatta.
Gli incentivi statali hanno dato una spinta forte al mercato, anche in assenza di una adeguata cultura: critica che va pure fatta allo stesso legislatore. Un aiuto al business è venuto anche dalla riduzione della soglia di ingresso in questo mercato, ovvero di accostamento delle aziende ai processi di automazione delle loro attività. Nel caso di Overlog del magazzino pensato come contesto fluido tra mondo produttivo in senso stretto e attività logistica legata al concetto di prossimità.
Si è investito invece piuttosto poco fino a oggi in automazione e anche da qui la sperequazione tra Italia ed estero. Il cambio generazionale, lentamente in atto, dovrebbe modificare la situazione, specialmente se accompagnato anche da una evoluzione culturale. L’azienda va sempre più vista come un ecosistema e la creazione di un patrimonio aziendale vero si prospetta come uno strumento di grande efficienza.
Marco Catizone, Head of Integration Space and Shared Services Unit di SICK
I sensori sono il punto di forza di SICK, realtà nata nel lontano 1946 in Germania. I sensori hanno la funzione essenziale di generare i dati dalla fonte, dal processo industriale. Ma generare dati non basta, occorre crearne sempre di più significativi ed elaborarli e aggregarli in maniera intelligente nel sensore stesso o nelle prime fasi dell’integrazione, in maniera decentralizzata. In questo modo è possibile trasformare i dati dei sensori in informazioni e, quindi, garantire valore e benefici per il cliente finale. Per esempio i sensori possono comunicare anche dati diagnostici, utili a essere elaborati per scopi manutentivi. Inoltre, devono potersi facilmente riconfigurare in modo automatico, per adattarsi alle variazioni di lavoro, tipiche di una produzione sempre più personalizzata e a piccoli lotti. Il concetto di Sensor Intelligence di SICK si sposa perfettamente con questa logica. Nell’ampio catalogo di più di 40 mila sensori dell’azienda, dai più semplici ai più complessi, c’è sempre l’attenzione alla qualità del dato, non solo in termini di affidabilità e sicurezza, ma anche di valore aggiunto. Inoltre, SICK si impegna a fornire anche prodotti software e servizi che aiutano a valorizzare ulteriormente l’informazione proveniente dai sensori, per connettere in maniera sempre più stretta l’OT con l’IT. Mentre in Italia gli investimenti in automazione legati al piano Industria 4.0 hanno avuto come obiettivo primario la riduzione dei costi di investimento, negli altri principali Paesi a noi vicini si dà più importanza allo sviluppo di un nuovo modo di produrre, che favorisca la resilienza, indispensabile per competere in uno scenario sempre più volatile. Molti clienti in ambito manifatturiero devono ancora acquistare piena consapevolezza dei benefici che le nuove tecnologie possono apportare al loro contesto produttivo.
Paolo Fanelli, IoT Sales Product di FANUC
FANUC è una società che si occupa anche di automazione industriale tramite un approccio molto strutturato, che assegna grande rilevanza alla centralizzazione operativa e alla sostenibilità green. In questa ottica stiamo offrendo il nostro contributo allo sviluppo dell’Industria 4.0 in Italia e preparando il terreno per l’Industria 5.0. Le prospettive sono buone, anche se abbiamo rilevato la necessità da parte dei vendor di dover calibrare un pò meglio l’offerta per esaltare le positività della digitalizzazione in ambito industriale evidenziandone i benefici non solo per chi gestisce impianti ma anche per gli imprenditori. Difficoltà, peraltro, che abbiamo riscontrato anche all’estero. Alle industrie non basta fare quel tanto pur di accedere agli incentivi economici statali, come hanno fatto molte PMI, occorre sposare una logica diversa. Cominciando, per esempio, da una migliore gestione dei dati raccolti dal campo in quanto sono un asset di valore strategico e quindi da impiegare al meglio in tutto il processo produttivo e decisionale. È ovviamente richiesto alla utenza uno grosso salto culturale e anche la disponibilità di macchine che interoperino tra di loro, quali quelle fornite da FANUC. Stando così le cose è mandatario focalizzarsi sulle applicazioni che generano valore per il cliente come, per esempio, quelle per ridurre la quantità di pezzi di ricambio in magazzino. È altresì auspicabile creare le condizioni per sinergie tra i partner tecnologici per trovare la soluzione migliore per quel cliente oppure introdurre nuovi servizi, come la manutenzione predittiva o il controllo qualità, spesso decisivi.
Al cliente non bisogna andare a dire io ti vendo prodotti IoT, ma una soluzione per il tuo problema oppure aiutarlo nel suo business: riduzione del TCO, aggiunta di nuovi servizi, efficientamento e altro. Il mercato c’è, va solo approcciato nel modo giusto. Come risposta universale all’IoT industriale, FANUC ha sviluppato il FIELD System (FANUC Intelligent Edge Link & Drive System), una piattaforma aperta che consente l’esecuzione di varie applicazioni IoT industriali, e non solo quelle, all’interno di una fabbrica incentrata sull’interconnessione di dispositivi come macchine utensili, robot, PLC, sensori… Attraverso la creazione di una rete interattiva di macchinari e attrezzature connesse, la piattaforma è in grado di sfruttare enormi quantità di dati e fornisce una soluzione per analizzarli in modo più rapido ed efficiente. Consente quindi di trarre informazioni intelligenti, per esempio fare previsioni sui comportamenti delle macchine o potenziali guasti. La piattaforma offre non solo ai costruttori di macchine utensili, ai produttori di sensori e dispositivi periferici la libertà di sviluppare le proprie applicazioni, ma anche a software house, centri di ricerca, università di poter creare nuovi algoritmi o utilizzare le nuove tecnologie quali intelligenza artificiale, machine learning, cloud… L’obiettivo del sistema FIELD è di raccogliere dati eterogenei da ogni dispositivo all’interno di una fabbrica (data lake), e offrire un sistema aperto e flessibile per lo sviluppo di nuove applicazioni anche business oriented garantendo anche una perfetta integrazione verso sistemi host superiori come ERP, MES, Scada. Il tutto assicurando il massimo livello di sicurezza: un sistema FIELD System non può essere venduto se non correlato ad un progetto di cybersecurity.
Aldo Campi, Amministratore di Stoorm5
Stoorm5 è una startup innovativa costituita nel 2015 nata con l’obiettivo di creare progetti e prodotti di IoT Industriale. Grazie al background tecnologico dei fondatori (sistemi distribuiti, software defined networking, applicazioni web e mobile, SIP, high performance computing) Stoorm5 ha realizzato un’innovativa piattaforma di Internet of Things che permette di ridurre enormemente costi e time-to-market per lo sviluppo di nuove applicazioni di monitoraggio e controllo remoto, anche grazie alla gestione real-time dell’invio di comandi a dispositivi remoti. Sulla base della piattaforma Stoorm5 sono già state realizzate diverse applicazioni, per esempio per il monitoraggio energetico di punti vendita, il monitoraggio di dispositivi in ambito ospedaliero e per il telecontrollo di dispositivi per il riscaldamento domestico. Inoltre, la società ha stretto importanti partnership, come quella con Siemens, per sviluppare in ambito industriale il concetto e il rispetto delle normative industriali e di resilienza. C’è ancora molto da fare per far crescere una cultura del digitale estesa alla fabbrica. Se manca una cultura del digitale gli investimenti non decollano o se decollano non necessariamente danno i risultati attesi. Questo accade anche per l’Industria 4.0, dove a mio avviso l’Italia registra un ritardo che va colmato quanto prima. Occorre anche avvalersi dei servizi di consulenti qualificati. Un problema che preoccupa è quello della sicurezza, ancora più difficile da affrontare in un contesto OT che in quello IT.
Alberto Servida, Professore Associato Università di Genova e Tesoriere Anipla
Dal 1956 Anipla – Associazione italiana per l’Automazione – è l’Associazione tecnicoscientifica di riferimento per l’automazione in Italia. Si propone di favorire e divulgare in Italia la conoscenza, lo studio e l’applicazione dell’automazione considerandola nei suoi aspetti tecnologici, economici e sociali, contribuendo in tal modo alla progressiva crescita. L’ultima indagine dell’Osservatorio Transizione Industria 4.0 (Politecnico di Milano, 2021) fornisce una fotografia dello ‘stato di salute’ del mercato per l’anno 2020. La ricerca mostra che, nonostante tutto, il mercato dell’Industria 4.0 (anche I4.0) è in crescita dell’8% rispetto al 2019 attestandosi a un valore stimato di 4,1 miliardi di euro con una previsione ottimistica del +12.15% per il 2021. La tecnologia IoT (connettività, acquisizione dati e macchinari) gioca un ruolo chiave e vale circa 2,4 miliardi in crescita del 4.5% rispetto al 2019. Seguono i settori industrial analytics (+9%, 685 milioni), cloud manufaturing (+20%, 390 milioni), servizi (consulenza operativa piuttosto che strategica, +8%, 275 milioni); advanced automation (+13%, 215 milioni); additive manufacturing (+8%, 91 milioni) e advanced HMI (+5%, 57 milioni). È importante osservare che nell’ambito dell’industrial analytics le soluzioni di IA (Intelligenza Artificiale) hanno registrato la crescita più marcata con un valore del +19% rispetto al 2019. Le risultanze dell’indagine sono in linea con il recente rapporto di Deloitte (2021) ‘L’importanza di un approccio ecosistemico alle iniziative Industry 4.0 – Una fotografia del settore manifatturiero italiano’ che fornisce un dato importante: il 63% delle aziende manifatturiere non ha sospeso gli investimenti per i progetti di smart manufacturing, anzi ha potenziato gli investimenti. Il rapporto evidenzia come le aziende italiane, nonostante abbiano capito l’importanza della trasformazione verso una manifattura avanzata, ancora oggi tendono a investire in progetti ‘quick win’ e solo il 27% delle aziende riesce a superare la fase pilota. Detto questo, un driver importante è legato all’esigenza di garantire una capacità produttiva flessibile, efficiente e veloce nell’adattarsi alle nuove esigenze del mercato per non perdere posizioni di competitività. Per le PMI, l’appartenenza a filiere manifatturiere guidate da grandi player OEM sicuramente rappresenta un fattore che favorisce l’adozione di soluzioni I4.0 per non per perdere posizioni privilegiate lungo la filiera della supply chain. A livello aziendale ci deve essere volontà a investire in innovazione a partire dal top management. I bisogni di miglioramento produttivo che vengono dal campo (shop floor), spesso, non sono sufficienti. Infatti, la transizione verso una manifattura avanzata richiede una radicale trasformazione non solo dei processi produttivi, ma anche di quelli aziendali. Ed è proprio per questa ragione che i tempi richiesti per raggiungere i risultati attesi non sono brevi. Un caso di studio esemplare è costituito da Rold, una PMI Lombarda, che ha iniziato il percorso di trasformazione ben prima che fosse proposto il paradigma I4.0. L’azienda già nel lontano 2016 aveva sviluppato internamente e installato una piattaforma di monitoraggio della produzione in tempo reale, Smart Fab. Il fattore più critico è quello culturale legato alle conoscenze e competenze non solo dei tecnici ma anche del management. Infatti, non si deve confondere il paradigma I4.0 con una o più tecnologie abilitanti, ma si deve comprendere che è necessario sfruttare l’integrazione e l’interazione delle tecnologie di automazione industriale in senso lato con quelle dell’ICT. Ed è per questo che ritengo che sia più corretto parlare di trasformazione/evoluzione industriale più che di rivoluzione industriale. Un altro fattore che può frenare la trasformazione del settore manifatturiero italiano delle PMI in un manifatturiero avanzato è legato alle difficoltà di quantificare i benefici conseguibili dall’implementazione di soluzioni I4.0 perché dipendono molto dalla realtà produttiva.